
When your generator runs but isn’t producing power, it usually comes down to a few key issues that can be fixed. The most common reasons include a loss of residual magnetism, tripped circuit breakers, or faulty components like the Automatic Voltage Regulator (AVR). In this article you are going to understand “Why Is My Generator Not Producing Power?” which will save you time and money by helping you identify and fix these problems quickly. This guide will walk you through each major reason, offering simple steps to troubleshoot and repair, so you can get your generator back to providing the power you need without any hassle.
10 Major Reasons Why Your Generator Is Not Producing Power
Generators are complex machines, and several factors could cause them to run without producing power. Understanding these common reasons will help you pinpoint the problem and take the right steps to fix it. Below, we’ll explore the top reasons like loss of residual magnetism, tripped circuit breakers, and more. Knowing these will not only save you from unnecessary headaches but also keep your generator in tip-top shape!. You can also check put our guide on top generators for emergency home backup power as well.
1. Loss of Residual Magnetism
When a generator fails to produce power, one of the most frequent culprits is the loss of residual magnetism. This might sound a bit technical, but don’t worry—we’ll break it down simply. Residual magnetism is crucial for a generator to start generating electricity. Without it, your generator won’t create the electromagnetic field needed for power.
What is Residual Magnetism?
Residual magnetism is a small amount of magnetism left in the iron core of the generator’s rotor after it has been turned off. This leftover magnetism is essential because it kick-starts the creation of an electromagnetic field when the generator is next started. When a generator starts, it relies on this residual magnetism to create the initial electrical current, which then boosts itself to full power. Without this magnetic field, the generator can’t produce electricity.
Causes of Residual Magnetism Loss
Residual magnetism can fade away for several reasons:
- Long Periods of Disuse: If a generator sits idle for too long, the residual magnetism can slowly disappear.
- Improper Shutdown Procedures: Turning off the generator while it is still connected to a load can drain the residual magnetism.
- New Generators and Transportation Vibrations: New generators can lose their residual magnetism during transport due to vibrations. Always check this when your generator arrives.
How to Restore Residual Magnetism
If your generator has lost residual magnetism, you can often restore it using a few simple tools:
- Using a Drill: Start the generator. Plug a corded electric drill into the generator’s outlet. While holding the drill trigger, spin the chuck of the drill quickly in the forward direction. This action can help regenerate the magnetic field.
- Using a 12-Volt Battery: Disconnect the AVR and brush wires from the generator. Connect a 12-volt battery to the rotor leads (positive to positive, negative to negative) for a few seconds. This should restore the magnetism.
If these steps sound daunting or don’t work, it’s wise to call a professional to assess and repair the generator safely.
2. Tripped Circuit Breakers
Another common reason why your generator might not produce power is tripped circuit breakers. Circuit breakers are safety devices that protect your generator from overloads or short circuits. When they trip, they cut off the electrical supply to prevent damage.
What Causes Circuit Breakers to Trip?
Circuit breakers can trip due to a few common reasons:
- Overloading the Generator: When you connect too many appliances or devices that draw more power than the generator can handle, the circuit breaker will trip to protect the system.
- Faulty Wiring or Short Circuits: Damaged or exposed wires can create short circuits, causing the breakers to trip.
Steps to Fix Tripped Breakers
To fix tripped breakers, follow these steps:
- Check and Reset the Breaker: Turn off all the appliances connected to the generator. Locate the breaker panel on your generator and check if any breakers are in the “off” position. If they are, flip them back to the “on” position.
- Understand Regular Breakers vs. GFCI Breakers: Generators often use Ground Fault Circuit Interrupter (GFCI) breakers for added safety. Unlike regular breakers, GFCI breakers detect even small leaks in the current and trip to prevent electrical shocks. If your GFCI breaker keeps tripping, there may be a problem with the wiring or the connected appliance.
Safety Precautions
It’s crucial not to bypass circuit breakers or attempt DIY repairs if you’re unsure. Circuit breakers are there to protect both you and your generator. If a breaker keeps tripping after resetting, or you notice any burnt smells or melted plastic, call a certified electrician. They can safely identify the root of the problem and ensure everything is working as it should.
3. Faulty Outlets and Power Cords
Your generator’s outlets and power cords are critical components in delivering power to your devices. If these parts are damaged or faulty, your generator might run, but no electricity will be available for use. Understanding how to identify and fix these issues will help keep your generator functioning safely and effectively.
Identifying Faulty Outlets
A faulty outlet can prevent power from reaching your appliances. Common signs of a faulty outlet include a blackened or melted appearance, which indicates overheating or electrical faults. To check if an outlet is working:
- Visual Inspection: Look for discoloration, melted plastic, or a burnt smell. These are clear indicators that the outlet may be damaged.
- Testing with a Multimeter: To be sure, use a multimeter to test the outlet. Set the multimeter to the voltage setting, insert the probes into the outlet slots (red in the live slot and black in the neutral slot), and check the reading. If the voltage reading is zero or fluctuates significantly, the outlet is likely faulty and needs replacing.
Common Power Cord Issues
Power cords are often overlooked, but frayed or damaged cords can be a significant problem. They can cause GFCI breakers to trip and may also present a risk of electric shock or fire.
- Inspecting Power Cords: Look for visible signs of wear, such as fraying, cuts, or exposed wires. If the insulation is compromised, it’s a hazard.
- Replacing Faulty Cords: If you find a damaged cord, it’s best to replace it. Ensure the replacement cord matches the power rating and specifications of your generator. Simply unplug the old cord and connect the new one securely.
Maintenance Tips
Regular maintenance checks can prevent many outlet and power cord issues:
- Routine Visual Checks: Periodically inspect all outlets and cords for signs of damage.
- Keep Cords Tidy and Protected: Avoid bending, twisting, or placing heavy objects on power cords, as these can lead to internal wire breaks.
- Check GFCI Breakers Regularly: Ensure that all GFCI outlets and breakers are working correctly by pressing the “test” button and making sure the “reset” button pops out.
4. Defective Automatic Voltage Regulator (AVR)
The Automatic Voltage Regulator (AVR) is a critical component of a generator, ensuring that it maintains a steady voltage output. If the AVR is defective, it can cause your generator to deliver unstable power or no power at all, which could damage your appliances.
What is an AVR and Why is it Important?
The AVR plays a key role in your generator’s operation by regulating the voltage output. It ensures that the generator provides a steady flow of electricity regardless of changes in load. This is crucial because inconsistent voltage can damage sensitive electronics and appliances. Without a working AVR, your generator might produce too high or too low voltage, leading to potential hazards or malfunction.
Signs of a Defective AVR
A faulty AVR can be identified by several symptoms:
- Unsteady Voltage Output: If you notice fluctuations in the power output or if the voltage is consistently too high or too low, the AVR could be the problem.
- Flickering Lights and Malfunctioning Appliances: Lights that flicker or appliances that behave erratically when powered by the generator may indicate that the AVR is not regulating the voltage properly.
- No Power Output: In some cases, a completely defective AVR will cause the generator to run without producing any electricity.
How to Replace a Faulty AVR
Replacing a faulty AVR is a straightforward process but requires caution to ensure safety:
- Turn Off the Generator and Disconnect All Loads: Make sure the generator is completely off and unplugged from any devices.
- Locate the AVR: Open the generator’s alternator cover to find the AVR, usually located near the control panel.
- Disconnect the AVR Wires: Take a picture of the connections to remember where each wire goes. Disconnect the wires carefully.
- Remove the Old AVR: Unscrew and remove the faulty AVR.
- Install the New AVR: Attach the new AVR by reconnecting the wires as per your reference picture and securing it with screws.
- Test the Generator: After replacement, start the generator and use a multimeter to check if the voltage output is stable.
If you’re unsure or uncomfortable performing this replacement, it’s best to seek professional help. Incorrect handling of electrical components can lead to further damage or safety hazards.
5. Poor or Loose Connections
Poor or loose connections in your generator can prevent it from producing power or cause it to operate inconsistently. These connection issues might seem minor but can lead to more serious problems if not addressed promptly. Understanding how to identify and fix these problems can save you from more extensive repairs down the line.
Common Connection Problems
Connections inside a generator can become loose or corroded over time, leading to poor performance. Some common connection problems include:
- Loose Wiring: Vibrations from the generator running can cause screws and wires to loosen over time, leading to poor electrical connections.
- Debris or Dirt Buildup: Dust, dirt, or small debris can accumulate around electrical connections, causing interference or poor contact.
- Oxidation or Corrosion: Exposure to moisture can lead to rust or oxidation on metal connectors, which can disrupt the flow of electricity and cause the generator to malfunction.
How to Inspect and Fix Poor Connections
Checking and fixing poor connections is a relatively simple process that can be done with some basic tools:
- Visual Inspection: Turn off the generator and disconnect it from any loads. Open the access panel and visually inspect the wiring and connections for any signs of looseness, dirt, or corrosion.
- Cleaning Connections: Use a wire brush or sandpaper to clean off any rust or corrosion from the connectors. Ensure the area is clean of debris or dirt that could affect the connection.
- Tightening Loose Connections: Use a screwdriver or pliers to tighten any loose connections. Be careful not to overtighten, as this could damage the wires.
- Testing with a Multimeter: After cleaning and tightening, use a multimeter to test the connections for continuity and ensure they are working correctly.
If you find severely corroded wires or connectors, consider replacing them to avoid future problems.
Best Practices for Ensuring Reliable Connections
To prevent future issues with poor or loose connections, it’s important to follow some best practices:
- Routine Maintenance: Regularly check the connections and wiring for signs of wear or damage.
- Keep It Clean: Ensure that the generator is kept in a clean, dry place to minimize dirt buildup and reduce the risk of corrosion.
- Use Dielectric Grease: Applying dielectric grease to electrical connectors can help prevent oxidation and maintain strong connections.
6. Broken or Worn Brushes
Carbon brushes are small but vital components of your generator. They help transmit electrical current from the rotating part of the generator (the rotor) to the stationary part (the stator). If these brushes become worn or broken, your generator may not produce electricity efficiently—or at all.
Role of Carbon Brushes in a Generator
Carbon brushes play a crucial role in the generator’s operation by maintaining electrical contact between the rotor and stator. As the rotor spins, these brushes ensure a steady flow of electrical current, allowing the generator to produce power. Over time, brushes can wear down due to friction, causing them to lose contact and reduce the generator’s efficiency.
Symptoms of Worn Brushes
Worn brushes are a common cause of power output problems in generators. Here are some signs that your generator’s brushes may need attention:
- Sparks or Electrical Arcing: If you see sparks or hear crackling noises from the generator, the brushes might not be making proper contact.
- Uneven Power Output: Fluctuating power output or drops in voltage can indicate that the brushes are not transferring electricity effectively.
- Grinding Noises: If you hear grinding sounds while the generator is running, it might be a sign that the brushes are worn down or not seated properly.
Replacing Worn Brushes
If you suspect that the brushes are worn out, replacing them can often solve the problem. Here’s how to do it:
- Turn Off the Generator and Disconnect It: Ensure the generator is turned off and disconnected from any power sources to avoid electric shocks.
- Locate the Brush Assembly: Open the alternator cover to locate the brush assembly. It is usually near the AVR and the rotor.
- Remove the Old Brushes: Unscrew the brush assembly and gently pull out the old brushes. Take note of their orientation and how they are connected.
- Inspect the Brushes and Assembly: Check the brushes for signs of excessive wear or damage. If they are worn down, cracked, or too small, they need to be replaced.
- Install New Brushes: Insert the new brushes into the assembly, ensuring they are positioned correctly. Secure them in place by tightening the screws.
- Reassemble the Generator: Put the alternator cover back on, ensuring all parts are securely fastened.
- Test the Generator: Start the generator and monitor for any signs of sparking, noise, or uneven power output to ensure the new brushes are working properly.
Safety Tip: Always wear protective gloves and use insulated tools when handling electrical components to avoid shocks.
7. Defective Capacitors
Capacitors are small but vital components in many generators, especially those without an Automatic Voltage Regulator (AVR). If a capacitor becomes defective, your generator may struggle to start or fail to produce power altogether. Knowing how to identify and replace a faulty capacitor is crucial for maintaining your generator’s performance.
What is the Function of a Capacitor in a Generator?
A capacitor in a generator plays a crucial role in both starting the engine and ensuring it runs smoothly. Here’s how it works:
- Starting the Generator: The capacitor stores electrical energy and releases it quickly to help start the generator’s engine. This initial burst of energy is essential, especially for larger generators that require more power to get moving.
- Regulating Power Output: During operation, the capacitor helps regulate the voltage output, ensuring a steady and reliable flow of electricity. This prevents fluctuations that could damage sensitive electronics or appliances.
Without a properly functioning capacitor, the generator may struggle to start or maintain a consistent power output, affecting its overall performance.
Signs of a Faulty Capacitor
A defective capacitor can cause several issues in a generator. Look for these signs to identify if the capacitor is faulty:
- Lack of Power Output: If the generator runs but doesn’t produce any power, the capacitor could be to blame. It might not be providing the necessary voltage to start the generation process.
- Unusual Noises: A faulty capacitor may cause the generator to emit a humming or buzzing noise. This noise is often due to the capacitor’s inability to regulate voltage properly.
If you notice any of these symptoms, it’s time to check the capacitor.
Testing and Replacing a Capacitor
Testing a capacitor’s health and replacing it, if needed, is a straightforward process. Follow these steps:
- Turn Off the Generator and Disconnect It: Ensure the generator is off and disconnected from all loads.
- Locate the Capacitor: Open the alternator cover to find the capacitor, typically a cylindrical or box-shaped component connected to the rotor.
- Discharge the Capacitor: Before testing, use an insulated screwdriver to discharge any remaining energy in the capacitor by bridging the terminals.
- Test with a Multimeter: Set your multimeter to the capacitance setting. Connect the probes to the capacitor terminals and check the reading. If the reading is significantly lower than the rated capacitance value (usually printed on the capacitor), it is faulty.
- Replace the Capacitor: If defective, remove the faulty capacitor by unscrewing it and disconnecting the wires. Connect the new capacitor in the same manner, ensuring all connections are secure.
- Reassemble and Test the Generator: Put the alternator cover back on, start the generator, and test for stable power output.
Safety Precaution: Always handle capacitors with care, as they can retain a charge even when the generator is off.
8. Excitation Circuit Issues
The excitation circuit is a critical part of a generator’s electrical system. It helps create the magnetic field needed to generate electricity. If there are issues with the excitation circuit, your generator may run but not produce any power. Understanding how to diagnose and fix these issues is vital to maintaining a functional generator.
Understanding the Excitation Circuit
The excitation circuit in a generator provides the necessary current to create a magnetic field within the alternator. Here’s a simple breakdown:
- How It Works: The excitation circuit supplies direct current (DC) to the rotor winding, creating a magnetic field. As the rotor spins, this magnetic field moves through the stator windings, inducing an alternating current (AC) that becomes the generator’s output.
- Role in Power Generation: Without a properly functioning excitation circuit, the magnetic field cannot be established, and no electricity will be generated.
A healthy excitation circuit is crucial for a generator to produce power reliably.
Common Problems in Excitation Circuits
Several issues can disrupt the excitation circuit and prevent the generator from generating power:
- Blockages: Dust, dirt, or other debris may obstruct the connections or moving parts in the circuit.
- Wiring Errors: Incorrect wiring connections or loose wires can cause the circuit to malfunction.
- Grounding Issues: Improper grounding or a short circuit can prevent the excitation circuit from functioning correctly.
Identifying these problems early can prevent more significant issues down the line.
How to Diagnose and Repair
Diagnosing and repairing excitation circuit issues requires careful attention. Here’s how you can do it:
- Use a Multimeter to Test Connections: Set the multimeter to the continuity or resistance setting. Test the excitation windings and connections for continuity. A broken connection or zero continuity indicates a fault.
- Inspect for Blockages: Open the generator’s access panel and inspect the excitation components for dust, dirt, or debris. Clean any obstructions using compressed air or a soft brush.
- Check for Wiring Errors: Ensure that all wires are connected correctly and securely. Refer to the generator’s manual for proper wiring configurations.
- Fix Grounding Issues: Use a multimeter to check for grounding problems. If you detect any irregularities, re-establish proper grounding by tightening loose connections or replacing faulty wires.
If you are not confident in diagnosing or repairing the excitation circuit yourself, it is best to consult with a professional technician to avoid any potential hazards.
9. Internal Engine Problems
The engine is the heart of your generator, and when it faces issues, it can significantly impact power production. Internal engine problems can stem from a variety of causes, from fuel system clogs to worn-out components. Knowing how to identify and address these issues will help keep your generator running smoothly.
Common Engine Issues Affecting Power Production
Several common engine problems can prevent your generator from producing power effectively:
- Fuel System Clogs: Dirty or clogged fuel lines, filters, or carburetors can restrict fuel flow, causing the engine to run poorly or not at all.
- Worn-Out Spark Plugs: Spark plugs ignite the fuel-air mixture in the engine. Worn or fouled spark plugs can lead to misfires, poor fuel combustion, and reduced power output.
- Air Filter Issues: A dirty or clogged air filter restricts airflow to the engine, leading to inefficient combustion and decreased performance.
These issues can cause the engine to struggle, directly affecting the generator’s ability to produce electricity.
Steps for Troubleshooting Engine Problems
Troubleshooting engine problems involves inspecting key components and performing regular maintenance:
- Inspect the Fuel System: Check the fuel tank, lines, and filters for clogs or debris. Clean or replace any components that appear dirty or blocked.
- Check the Spark Plugs: Remove the spark plugs and examine them for signs of wear, such as black carbon deposits or a damaged electrode. Replace any spark plugs that appear fouled or worn out.
- Clean or Replace the Air Filter: Remove the air filter and inspect it for dirt and debris. If it looks dirty, clean it with compressed air or replace it with a new one.
- Perform Regular Maintenance: Change the oil regularly and check other engine components for signs of wear. Regular oil changes keep the engine lubricated and running smoothly, preventing unnecessary wear and tear.
Regular maintenance and inspections can prevent many engine-related problems, keeping your generator running efficiently.
When to Call a Professional Mechanic
While some engine problems can be fixed with DIY maintenance, others require professional expertise:
- Persistent or Complex Issues: If you have repeatedly tried to fix the problem and the generator still isn’t running correctly, it’s time to call a professional.
- Unfamiliar Noises or Smoke: Loud knocking noises, grinding, or excessive smoke from the engine can indicate serious issues that need professional attention.
- Oil Leaks or Major Component Failures: If you notice oil leaking from the engine or suspect a major component like the crankshaft or piston is damaged, consult a mechanic immediately.
Calling a professional can prevent further damage and ensure your generator is repaired safely and correctly.
10. Defective Circuit Breakers
Circuit breakers play a critical role in protecting your generator’s electrical system from overloads or short circuits. When these breakers become defective, they can prevent power output even when the generator is running. Understanding how to diagnose and replace defective circuit breakers will help you maintain a safe and efficient generator.
How Defective Breakers Impact Generator Performance
Defective circuit breakers can disrupt your generator’s power output by breaking the electrical connection, even when there is no overload:
- Prevent Power Flow: A faulty breaker may fail to maintain a proper connection, stopping electricity from flowing from the generator to the connected appliances.
- False Tripping: Defective breakers might trip unexpectedly, shutting off power even under normal load conditions, which can be frustrating and cause unnecessary downtime.
Recognizing these signs can help you identify a defective breaker early and take corrective action.
Diagnosing a Defective Breaker
To diagnose a defective circuit breaker, follow these steps:
- Turn Off the Generator and Disconnect Loads: Ensure the generator is off and unplugged from any connected appliances to avoid electrical hazards.
- Inspect the Breaker Panel: Open the generator’s breaker panel and visually inspect each breaker for signs of wear, burning, or melting.
- Test the Breakers with a Multimeter: Set your multimeter to the continuity or resistance setting. Place the probes on the breaker terminals; if there is no continuity or the reading is out of range, the breaker is likely defective.
- Check for Loose Wires: Ensure that all wires connected to the breaker are tight and secure. Loose wires can also cause breakers to trip or fail.
If the breaker is found to be faulty, replacing it is the next step.
Replacing Defective Breakers
Replacing a defective circuit breaker requires care to avoid electrical hazards. Here’s how to do it safely:
- Turn Off the Generator and Disconnect Power Sources: Ensure the generator is completely off and disconnected from any power sources.
- Open the Breaker Panel: Use a screwdriver to remove the panel cover and access the circuit breakers.
- Remove the Faulty Breaker: Carefully disconnect the wires attached to the defective breaker. Take note of the wire connections for proper reinstallation.
- Install the New Breaker: Insert the new breaker into the panel, reconnect the wires, and ensure they are securely tightened.
- Close the Panel and Test the Generator: Replace the panel cover, start the generator, and check if the new breaker operates correctly without tripping.
Safety Tip: Always wear rubber gloves and use insulated tools when handling electrical components to avoid shocks.
Final Words!
In conclusion, understanding why your generator isn’t producing power can save you time, money, and frustration. From common issues like loss of residual magnetism and tripped circuit breakers to more complex problems involving defective capacitors, excitation circuits, and internal engine components, each problem has a specific solution that can be tackled with the right knowledge and tools. Regular maintenance and proper handling can prevent many of these issues from arising in the first place.
For problems that are beyond DIY repair, such as complex engine malfunctions or major electrical issues, it’s always best to consult a professional. This ensures that repairs are done safely and effectively, preventing further damage or costly mistakes. Generators are valuable machines, and keeping them in good working order is essential for reliable power supply.
By addressing these 10 major reasons, you can restore your generator’s performance and ensure it is ready when you need it most. Remember, a little preventive care goes a long way in keeping your generator running smoothly.
Related FAQs
What Are The Signs Of A Faulty Generator Capacitor?
Signs include lack of power output, unusual noises, or irregular voltage levels.
Can Loose Connections Cause A Generator To Stop Producing Power?
Yes, loose or corroded connections can disrupt power generation and need fixing.
How Do I Know If My Generator’s Spark Plug Needs Replacement?
If your generator is hard to start or runs unevenly, the spark plug may need replacement.
Are GFCI Breakers Necessary For Generators?
Yes, GFCI breakers help prevent electrical shocks and protect the generator from overloads.
Is It Safe To Bypass A Tripped Circuit Breaker?
No, bypassing a tripped breaker is dangerous and can cause severe damage or accidents.
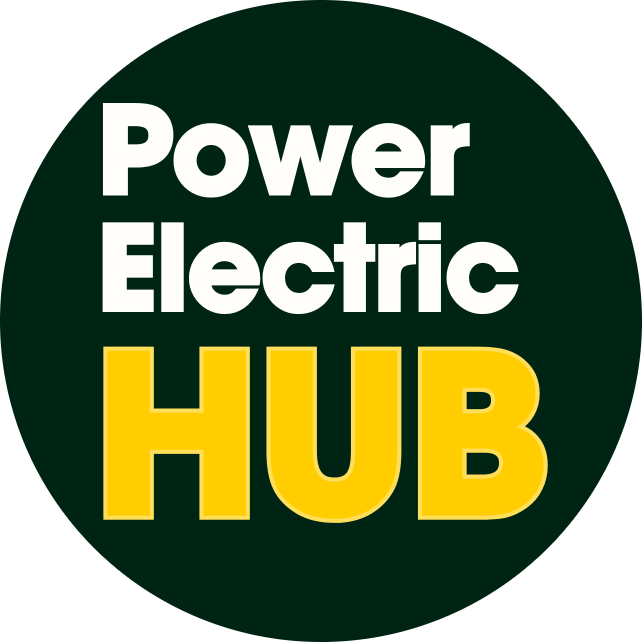
At our core, we’re a group of passionate generator, inverter, solar energy, battery enthusiasts. We dive deep into the world of tech, especially when it’s about powering your home, RV or outdoors. We try to provide as much value to the readers with our information and how to blog articles as possible. For affiliate articles our honest and transparent reviews of essential tech products are rooted in real-world experience. We take great satisfaction in offering unbiased evaluations, ensuring that you can make informed decisions when investing in your desired techs.